Unveiling the Secrets of Insert Molding: Techniques and Applications
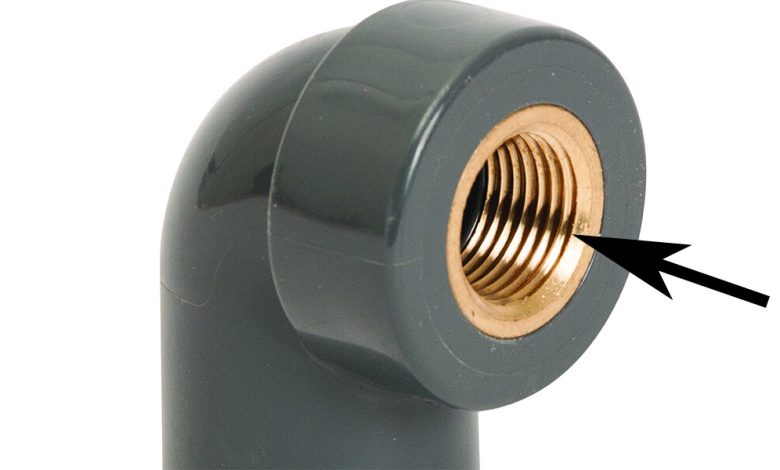
In the realm of modern manufacturing, where efficiency, precision, and versatility are paramount, insert molding stands out as a transformative technique. It merges multiple materials seamlessly to create intricate components with enhanced functionality and durability. As industries continue to evolve, understanding the intricacies of insert molding becomes essential for manufacturers seeking to stay ahead of the curve. This article delves into the secrets of insert molding, exploring its techniques, applications, and the myriad of benefits it offers.
Understanding Insert Molding
At its core, insert molding is a specialized form of injection molding that involves encapsulating pre-formed components, known as inserts, within a molded part. These inserts can be made from various materials such as metals, plastics, ceramics, or even electronic components. Unlike traditional assembly methods, which require multiple steps and materials, insert molding consolidates the manufacturing process into a single operation, resulting in cost savings and improved efficiency.
Techniques of Insert Molding
Overmolding: Overmolding is a common technique used in insert molding where a base substrate or part is encapsulated with a second material. This technique is often employed to add a soft-touch grip, enhance aesthetics, or provide additional functionality to the final product. Overmolding can be particularly useful in consumer electronics, automotive interiors, and medical devices.
Compression Insert Molding: Compression insert molding involves placing inserts into a mold cavity and then compressing them with molten material to form the final part. This technique is well-suited for molding large or irregularly shaped inserts and is commonly used in automotive and aerospace applications.
Rotary Insert Molding: Rotary insert molding is a specialized technique where the mold rotates during the injection molding process. This rotation allows for the insertion of multiple inserts into the mold cavity, enabling the production of complex, multi-component parts with high precision. Rotary insert molding is often used in the production of electronic connectors, switches, and automotive components.
Transfer Molding: Transfer molding is a variation of insert molding where the inserts are placed into a heated mold cavity before the molten material is transferred into the cavity under pressure. This technique is suitable for molding intricate parts with precise dimensions and is commonly used in the production of electrical connectors, seals, and gaskets.
Benefits of Insert Molding
Enhanced Structural Integrity: By encapsulating inserts within the molded part, insert molding creates a strong, seamless bond between materials, resulting in improved structural integrity and durability. This eliminates the need for additional fasteners or adhesives, reducing the risk of component failure.
Cost Efficiency: Insert molding offers significant cost savings compared to traditional assembly methods by consolidating multiple manufacturing steps into a single operation. This reduces labor costs, assembly time, and material waste, resulting in overall cost optimization.
Design Flexibility: Insert molding enables manufacturers to create complex, multi-material components with greater design flexibility. This versatility allows for the integration of diverse materials, such as metals, plastics, and electronics, to meet specific performance requirements and aesthetic preferences.
Improved Product Performance: By integrating different materials within a single molded part, insert molding enhances product performance and functionality. This enables manufacturers to optimize product performance for various applications, leading to increased customer satisfaction and market competitiveness.
Applications of Insert Molding
Insert molding finds widespread application across various industries and products, including:
- Automotive components (e.g., sensors, connectors, dashboard switches)
- Consumer electronics (e.g., circuit boards, connectors, housings)
- Medical devices (e.g., catheters, surgical instruments, fluid delivery systems)
- Aerospace and defense (e.g., aircraft interior components, avionics housings, UAVs)
- Consumer goods (e.g., appliance components, electronic enclosures, sporting equipment)
Conclusion
In conclusion, insert molding represents a powerful and versatile manufacturing technique that offers numerous benefits, including enhanced structural integrity, cost efficiency, design flexibility, and improved product performance. By understanding the techniques and applications of insert molding, manufacturers can unlock its full potential to create innovative, high-quality components for a wide range of industries. As technology continues to advance, insert molding is poised to play an increasingly integral role in shaping the future of manufacturing.